Why Choose This System?
Industrial-Grade Durability – Withstands heavy machinery, foot traffic, and harsh chemicals.
Seamless & Abrasion-Resistant – Long-lasting epoxy formula for superior strength.
Customizable Aesthetic – Available in various colors and finishes to match your space.
Low Maintenance & Easy to Clean – Practical and functional for industrial environments.


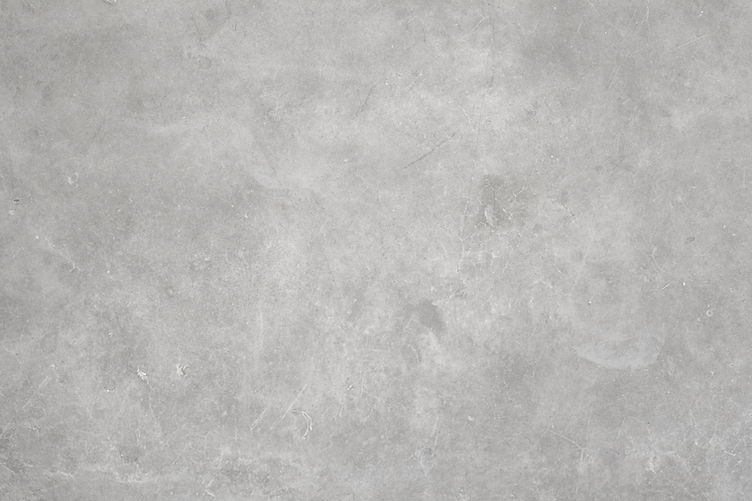
BETTER OPTION: Tru Solid NanoX Industrial Coating System

The Tru Solid NanoX Industrial Coating System provides a robust and seamless finish designed for demanding industrial spaces. Built to handle heavy traffic, machinery, and chemicals, this system offers both strength and style. Explore our gallery to see how the Tru Solid NanoX can transform your space with its high-performance durability and clean, polished look. Get inspired to upgrade your industrial flooring with a solution that stands the test of time.

Tru Solid NanoX Industrial Coating System Process
For industrial and commercial spaces that require exceptional durability and performance, the Tru Solid NanoX Industrial Coating System is an ideal choice. This advanced coating system is designed to provide a long-lasting, high-quality finish that can withstand the rigors of heavy use and demanding environments. Here’s a comprehensive look at the detailed process involved:
Installation Steps Explained:

STEP ONE | Surface Preparation:
The process begins with meticulous surface preparation to ensure a strong bond between the concrete and the coating system. We start by thoroughly cleaning the concrete surface, removing any dirt, oil, old coatings, and other contaminants that could affect adhesion. Specialized equipment such as diamond grinders or shot blasters is employed to mechanically prepare the surface. This equipment etches the concrete and opens its pores, enhancing the adhesion of the coating. After the surface has been ground, it is carefully vacuumed to remove all dust and debris, leaving a clean, textured base ready for the coating application.

STEP TWO | Crack Repair:
Once the surface is prepared, we focus on repairing any cracks, joints, or holes present in the concrete. High-strength epoxy fillers or concrete patching compounds are used to fill these imperfections. This step is crucial to ensure a smooth, even surface that prevents any issues with the coating’s adhesion. The repaired areas are meticulously sanded and smoothed to blend seamlessly with the surrounding concrete, creating a uniform surface that supports the integrity of the final coating layers.
STEP THREE | Basecoat Application of Tru MVB 100 Solid Epoxy:
With the surface prepped and repaired, we apply the Tru MVB 100 Solid Epoxy Basecoat. This basecoat serves as a moisture vapor barrier, preventing moisture from seeping through the concrete and causing problems such as bubbling or delamination. The epoxy is evenly applied using a squeegee and roller, ensuring a consistent thickness and coverage across the entire floor. This foundational layer not only protects the concrete but also enhances the bond between the surface and the subsequent topcoats.

STEP FOUR | Topcoat #1 with Industrial Epoxy Pigmented Layer:
After the basecoat has fully cured, we proceed with the first topcoat, which is a pigmented industrial epoxy layer. This topcoat provides a solid, uniform color while offering superior resistance to chemicals, abrasion, and heavy traffic. The pigmented epoxy is carefully applied using a roller or squeegee, ensuring an even and smooth finish. This layer is essential for both the aesthetic appeal and the durability of the flooring, making it suitable for the demanding conditions of industrial and commercial environments.

STEP FIVE | Topcoat #2 with High Wear Polyurea with Anti-Slip and AlumX High Wear Additive:
The final step involves the application of a high-wear polyurea topcoat. This topcoat is available in a range of finishes, including matte, satin, and gloss, depending on your preference. It is mixed with Tru Anti-Slip and AlumX High Wear Additive to provide an additional layer of protection against slip hazards and wear. The polyurea topcoat is applied with precision using specialized tools, ensuring a seamless, high-performance finish that can withstand heavy use, abrasion, and exposure to chemicals. This final layer not only enhances the floor’s durability but also improves safety and longevity.
Why should you choose Tru-Grit for your industrial project?
The Tru Solid NanoX Industrial Coating System offers a comprehensive, high-quality flooring solution designed to meet the rigorous demands of industrial and commercial applications. By following this detailed process, we ensure a durable, aesthetically pleasing finish that provides excellent protection and performance. From meticulous surface preparation to the final topcoat application, every step is carefully executed to deliver a flooring solution that stands up to heavy traffic, harsh conditions, and the test of time.
Color Options
Tru-Solid Commercial Color Options
Explore our range of base color options to find the ideal match for your project. We provide 5 complimentary solid color choices to get you started, along with premium upgrade options for those seeking something truly unique. Browse both our standard and premium selections to discover which best suits your style and project requirements. Choose the base color that enhances your space and makes it stand out.